The Latest from Wallaces Farmer
sprayer in field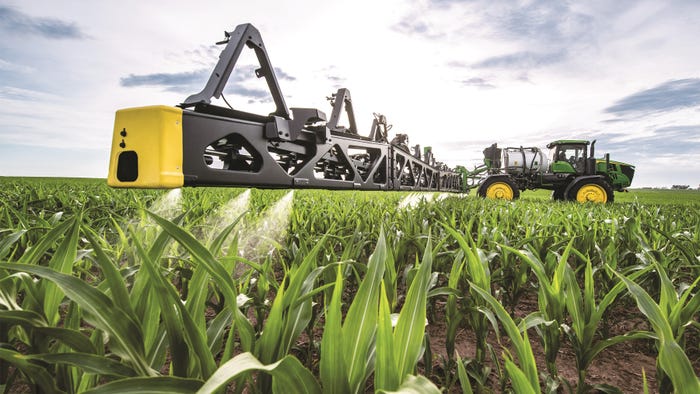
Management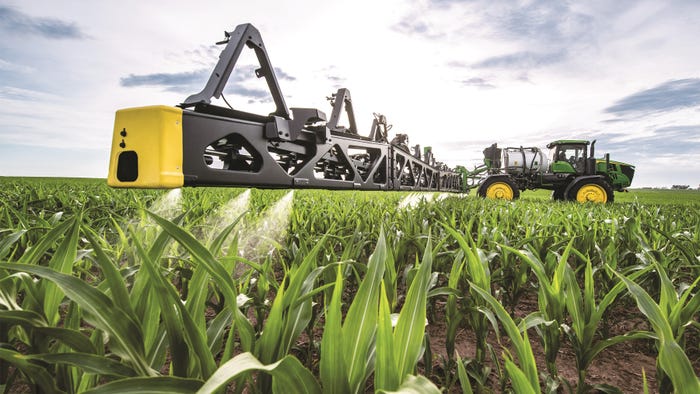
Where precision spraying systems fitWhere precision spraying systems fit
Postemergence foliar herbicide savings can be achieved, but soil residual herbicides and nonchemical approaches also are needed, an Extension weed scientist says.
Market Overview
Contract | Last | Change | High | Low | Open | Last Trade |
---|---|---|---|---|---|---|
Jul 24 Corn | 452 | unch — | 453 | 450.5 | 451.75 | 12:30 PM |
Jul 24 Oats | 354.25 | +3.25 | 356.75 | 352.25 | 352.25 | 11:21 AM |
May 24 Class III Milk | 18.33 | +0.15 | 18.37 | 18.25 | 18.28 | 12:26 PM |
Jul 24 Soybean | 1174.75 | -5 | 1181 | 1172.5 | 1179 | 12:30 PM |
Aug 24 Feeder Cattle | 258.3 | +2 | 258.8 | 254.25 | 256.425 | 06:04 PM |
May 24 Ethanol Futures | 2.161 | unch — | 2.161 | 2.161 | 2.161 | 09:38 PM |

Copyright © 2019. All market data is provided by Barchart Solutions.
Futures: at least 10 minute delayed. Information is provided ‘as is’ and solely for informational purposes, not for trading purposes or advice.
To see all exchange delays and terms of use, please see disclaimer.
All Wallaces Farmer
Subscribe to receive top agriculture news
Be informed daily with these free e-newsletters